Revolutionising Micropowder Production
We harness the power of non-contact gas-dynamic resonance disintegration technology to develop micropowders that surpass conventional materials. With our innovative approach, we provide solutions that enhance your product's properties, giving you a competitive edge in the market.
Building new solutions that reduce the workload on employees
Lorem ipsum dolor sit amet, consectetur adipiscing elit. Curabitur sit amet eros blandit, hendrerit elit et, mattis purus. Vivamus commodo suscipit tellus et pellentesque.
Mattis purus. Vivamus commodo suscipit tellus et pellent. Curabitur sit amet eros blan esque.
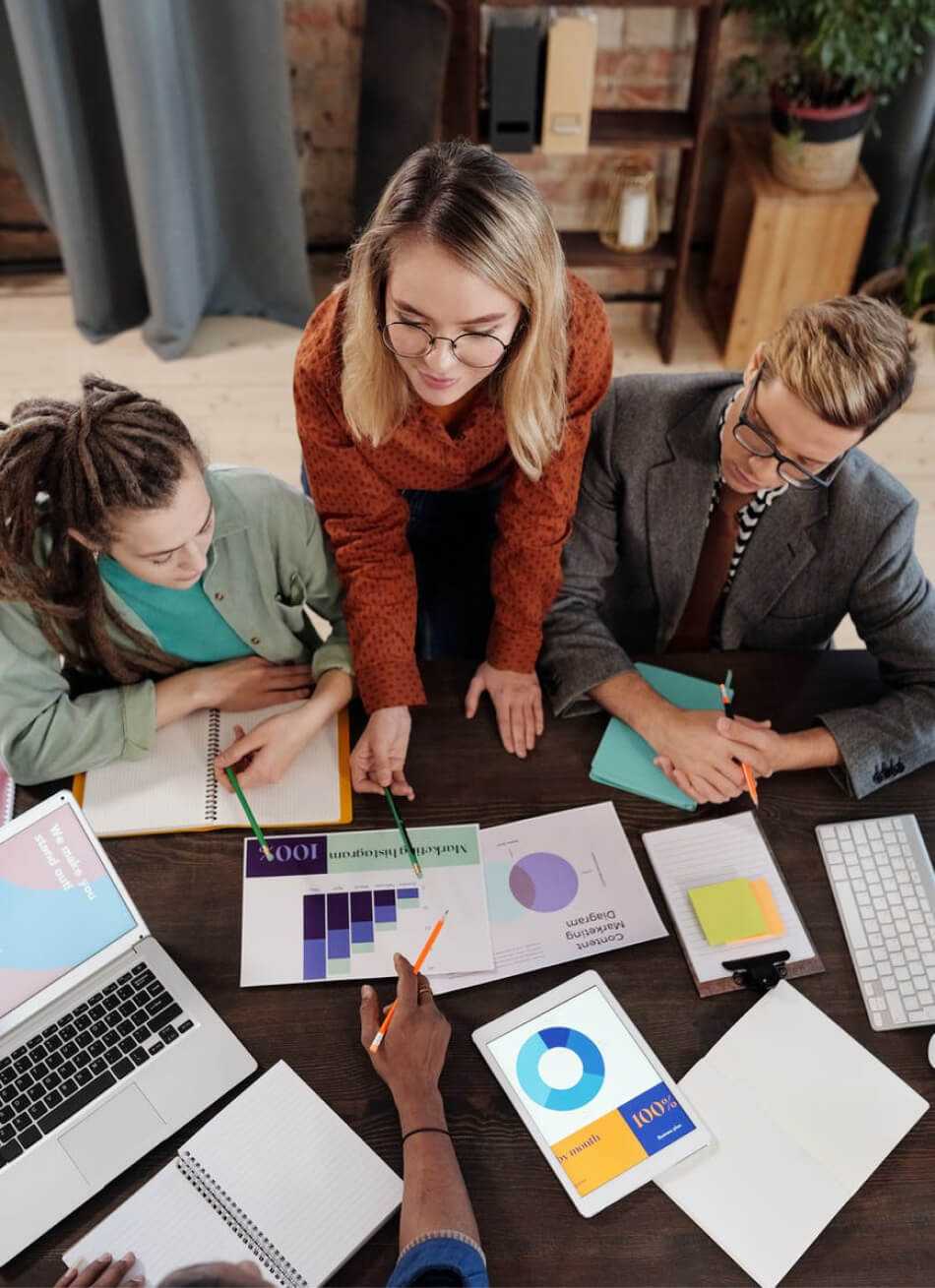
Assessing risk with artificial inteligence software
Lorem ipsum dolor sit amet, consectetur adipiscing elit. Curabitur sit amet eros blandit, hendrerit elit et, mattis purus. Vivamus commodo suscipit tellus et pellentesque.
Mattis purus. Vivamus commodo suscipit tellus et pellent. Curabitur sit amet eros blan esque.
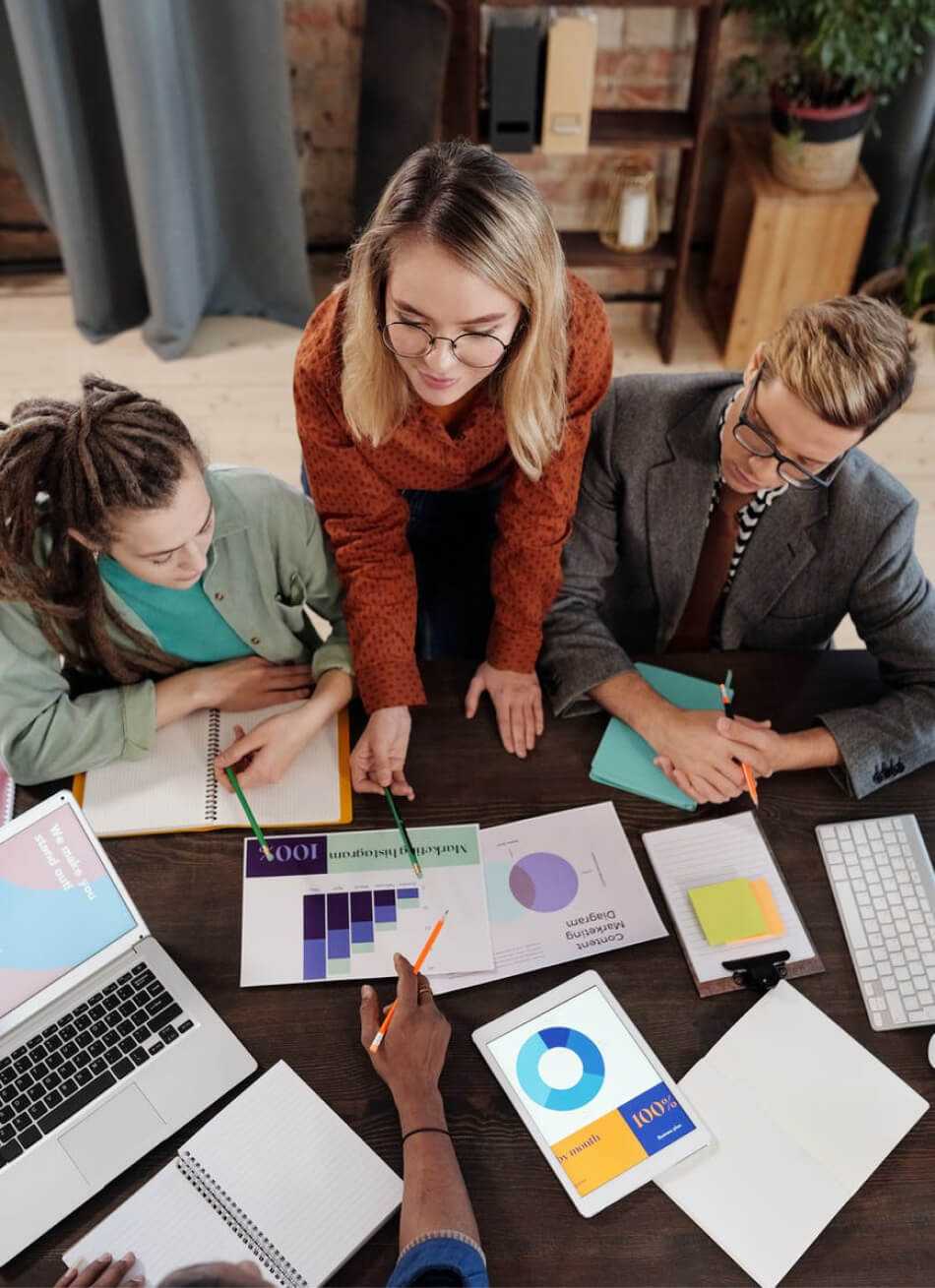
Our Technology
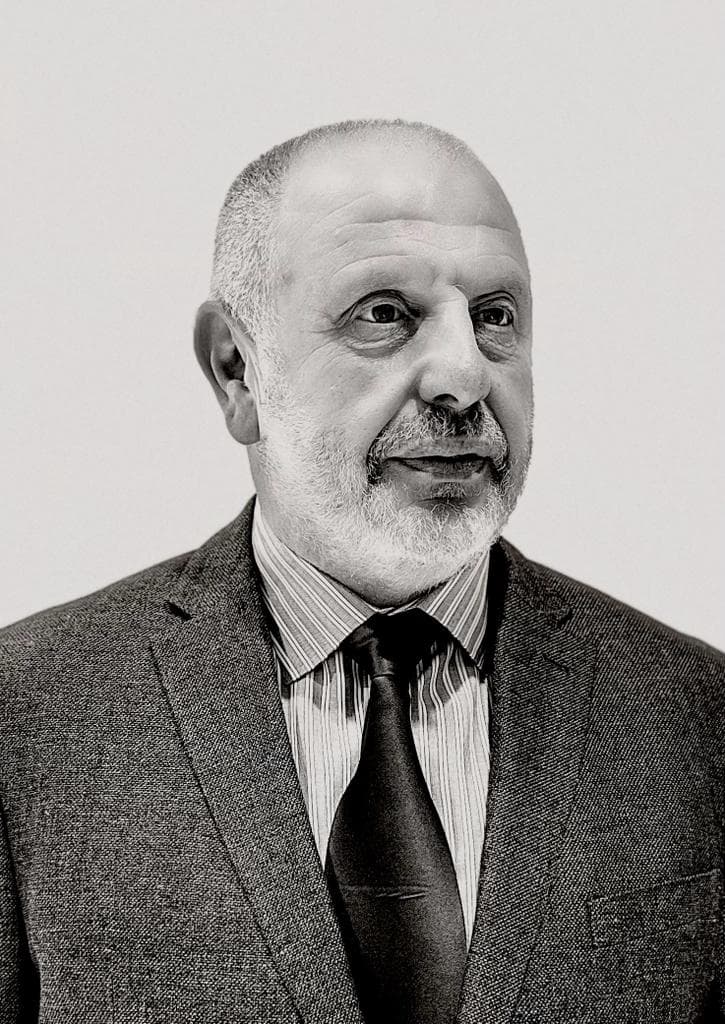
.jpg)
Always a step ahead
We use cutting-edge research to create micropowders that are far superior to the materials now available. We offer creative solutions to improve your product's qualities and give you an edge in the marketplace.
About Us
Innovative and Patented Technology
Gas-Dynamic Vortex Micronization
Versatile Material Compatibility
High-Quality Ceramic Linings
Multiple GDVM Mill Models
Universal Material Grinding
Precise Fraction Separation
Low Energy Consumption and High Productivity
.jpeg)
Technology
Our Products
Our cutting-edge solutions in micropowders production revolutionize industries and push the boundaries of what is achievable.
Get in touch
Kindly inform us of your required micropowders, and our team of experts will provide customized solutions and technical support to ensure the optimal performance of our micropowders in your specific application.